In the fast-paced world of manufacturing, efficiency and reliability are crucial. As products become more advanced, the need for precise and secure fastening solutions continues to grow. Clips play a fundamental role in assembling various components, ensuring that parts remain securely attached throughout their lifespan. However, manufacturers often face challenges in automating clip insertion due to slight variations in clip geometry, material inconsistencies, and production complexities. This is where RoboClip stands out as a game-changer.
Is My Clip Compatible with RoboClip?
Most clips with a pointed shape are compatible with the standard RoboClip machine. Designed with flexibility in mind, our tool can be customized to fit your specific clip type. Whether you’re working with unique shapes or sizes, minor modifications can ensure a perfect fit. Contact us today to discuss your application, and we’ll guide you through the process.
Can RoboClip Handle Other Clip Types?
Absolutely! With over three decades of experience in clip automation, our custom machine-building team at Innovative Automation thrives on solving complex challenges. Connect with one of our application specialists to explore how RoboClip can streamline your production process.
The Role of Arrowhead-Style Clips in Assembly
Arrowhead-style clips are widely used across industries due to their ability to provide strong and reliable attachment without requiring additional fasteners. These clips, commonly known as A Clips, V Clips, Bird’s Beak, IP Clips, Grille Clips, and Instrument Panel Clips, offer manufacturers a cost-effective and streamlined method for assembly. Because these clips come in different shapes, sizes, and materials, it is essential for automation systems to be flexible enough to handle various clip types without frequent reconfiguration.
RoboClip is designed with this versatility in mind, allowing manufacturers to automate clip placement efficiently. By accommodating a broad spectrum of arrowhead-style clips, RoboClip eliminates the need for multiple machines or extensive retooling, resulting in significant time and cost savings.
Overcoming Variability in Clip Manufacturing
One of the biggest hurdles in clip automation is managing slight inconsistencies that arise during the injection molding process. Since many clips are produced using multi-cavity molds, variations in cooling rates, material flow, and tooling precision can lead to defects such as flash, short shots, warping, and sink marks. Even the smallest imperfections can impact a clip’s ability to fit properly within an automation system, leading to frequent jams, reduced cycle times, and increased downtime.
RoboClip’s patent-pending anti-jam technology directly addresses these issues. Unlike traditional feeder systems that rely on mechanical precision and high-tolerance guides, RoboClip intelligently adapts to minor variations in clip geometry. This innovation drastically reduces disruptions and ensures a consistent flow of clips into the assembly process, improving production efficiency and minimizing waste.
Common Challenges in Clip Production
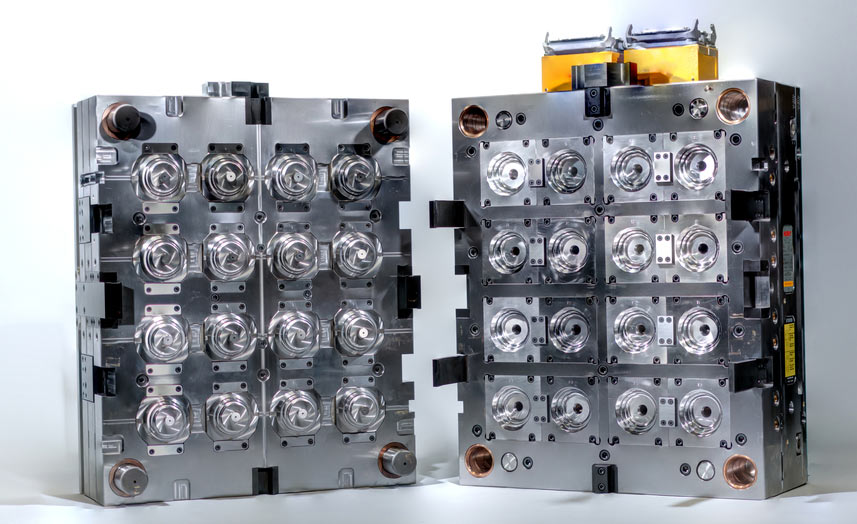
CLIP ISSUES
Injection-molded clips created in multi-cavity molds often have slight variations. Defects like flash, short shots, warping, and sink marks can compromise clip quality and cause jamming in downstream equipment like bowl or blow feeders.
How RoboClip Solves These Issues
RoboClip’s patent-pending anti-jam technology is specifically designed to address common molding challenges. Instead of relying on tight-tolerance guides and air jets, RoboClip intelligently adapts to clip geometry and resolves jams quickly and efficiently.
The Challenges of Handling Injection-Molded Parts
Beyond clip-related challenges, manufacturers must also consider the potential issues that arise with injection-molded parts. Components that require clips often face dimensional variations due to shrinkage, uneven cooling, or improper handling during storage. These factors can cause misalignment or bending of clip towers, which in turn affects the accuracy of clip insertion.
Traditional robotic systems struggle to accommodate these variations, often requiring manual intervention or extensive reprogramming to compensate for shifting clip positions. This not only adds labor costs but also extends downtime, which can significantly impact production throughput.
RoboClip offers a smarter alternative by integrating a user-friendly programming interface that enables operators to adjust clip insertion points in seconds. Instead of reprogramming an entire robotic work cell, users can make quick modifications through an intuitive system, ensuring seamless production without sacrificing accuracy.
Challenges with Parts and Production
PART ISSUES
Injection-molded parts can also face challenges, particularly when produced in family or multi-cavity molds. Variations during cooling and shrinkage, as well as improper stacking in dunnage or racks, can cause bending of clip towers or posts.

IMPACT ON PRODUCTION
Bent clip towers can disrupt automation, requiring skilled labor to reprogram insertion points for standard six-axis robotic systems. RoboClip overcomes this obstacle with a user-friendly programming interface. Clip positions can be verified and adjusted in seconds, reducing downtime and eliminating the need for extensive reprogramming.
How RoboClip Enhances Efficiency
Elevate Your Clip Production with RoboClip
Manufacturers should not have to struggle with inefficiencies caused by clip inconsistencies and automation challenges. RoboClip provides an intelligent, adaptable solution to improve production speed, reduce errors, and integrate seamlessly into existing processes.
Are you ready to enhance your clip production workflow? Contact our team today to explore how RoboClip can be customized to meet your specific manufacturing needs.